Electric Road Systems: Zero-Emission Road Transport in a Different Way
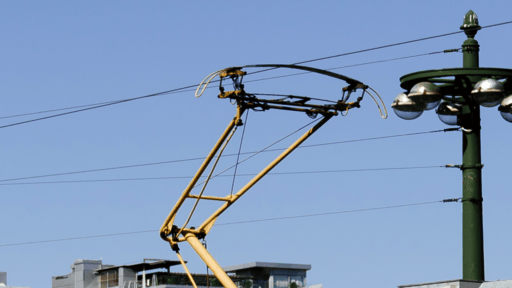
Truck manufacturers are tirelessly working to offer electric or hydrogen fuel cell-powered trucks and semi-tractors with increasingly larger operational ranges. Range (and still high prices) remains the biggest limitation in the widespread adoption of EV and FCEV vehicles in the transport and logistics industry. Insufficient charging infrastructure along highways and expressways also continues to be an issue. Hence, alternative projects collectively known as Electric Road Systems (ERS) are being explored. What are they all about?
The ranges of electric semi-trailers are steadily increasing. For example, the Mercedes-Benz eActros 600 provides a range of around 500 km on a single charge, thanks to its 600+ kWh battery. Similarly, electric versions of Volvo trucks (models FH and FM) can travel up to 300 km on a single charge, depending on battery configurations. These numbers are significant for daily operations, but the availability of charging stations is another crucial factor.
A few years ago, when electric and hydrogen trucks were just entering the market and the direction of automotive development was unequivocally zero-emission, alternative solutions for road freight transport emerged. These aimed to provide continuous electrical power to moving trucks, eliminating the limitations of low battery capacity and the need for stops to recharge.
ERS: Overhead Line Systems
The most well-known alternative electric road system (ERS) involves an overhead line configuration. This system installs poles along the road with a catenary wire strung between them. Specially adapted electric or hybrid trucks can draw electrical power from this wire using a pantograph. This solution is reminiscent of the technology successfully used in city trolleybuses for decades.
One of the most notable projects utilizing this solution is eHighway, implemented by the German company Siemens. In 2017, the company began tests on a ten-kilometer section of the A5 motorway between Frankfurt Airport and Darmstadt. Another test commenced on a five-kilometer section of the A1 motorway between Reinfeld and Lübeck, and a third on the B 462 national road between Kuppenheim and Gaggenau. The results were promising enough that the National Platform for the Future of Mobility (NPM), an organization operating under the German transport ministry, suggested that by 2030, a 4000-kilometer network of eHighway systems should be built along key roads.
The advantage of ERS with overhead lines is that it builds upon a technology in use since 1882 (when Werner Siemens presented the prototype of the first trolleybus) and is continuously modernized. It also wouldn’t require significant changes to existing road infrastructure, as the overhead line does not necessitate new road surfaces, and traditional vehicles can still use the roads alongside the overhead line system. However, the need to build the catenary network (still seen as too costly by highway operators) and adapt trucks and semi-trailers to draw power from the network (installing pantographs) remains a limitation.
ERS: Ground-level Power Supply Systems
While the eHighway system is based on the technology powering trolleybuses, the next ERS discussed in this article takes inspiration from solutions used in underground trains. This system features a rail embedded in the road surface, which transmits electrical power to the vehicle via a special connecting arm. Various companies have been developing this system since 1996. In the French city of Bordeaux, a tram powered by a third rail embedded in the road, developed by Alstom, has been operating since 2022 (safe for other road users). This configuration is also being considered for powering electric cars in France: a test section is set to be operational in 2024, with trials ending after three years. The ground-level power supply system is also in use in Sweden, where it was launched on a road near Arlanda Airport in Stockholm. This solution is advantageous because it can be used by both trucks and smaller commercial vehicles, and it has a smaller impact on the landscape (no poles and wires). However, the higher construction cost and road maintenance issues, particularly in poor weather conditions, are significant challenges.
ERS: Inductive Charging Systems
The inductive system, where coils are embedded in the road surface and vehicles are equipped with receiving coils, is the last ERS considered. South Korea implemented several city bus lines powered this way between 2009 and 2016, but the commercialization of this technology was unsuccessful. This system has its advantages: it does not alter the landscape and has greater durability because the power transfer occurs without physical connection. However, the implementation costs are very high, as it requires replacing the entire road surface with one containing coils, unlike the ground-level power supply system where only the rail needs to be embedded.
Despite promising results from each ERS and ongoing plans and work in Germany, France, and Sweden, it is difficult to predict whether these projects will be realized on the planned scale. The range of electric trucks is continuously increasing, and the charging infrastructure in European countries is expanding not only in major cities but also along intercity routes and highways. Perhaps the term “e-road”will more likely describe roads with charging stations as densely distributed as gas stations, rather than any specific ERS system. As always, time will tell.